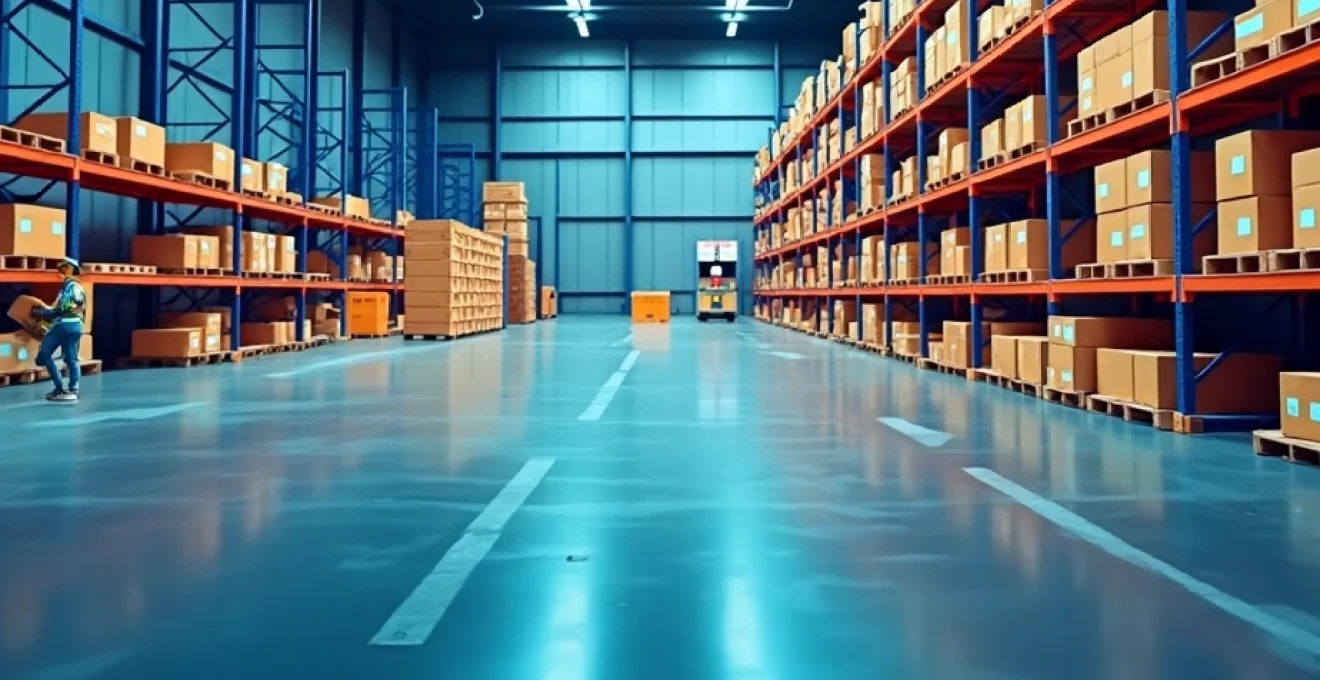
Efficient warehouse operations are the backbone of successful supply chain management. As businesses strive to meet increasing customer demands and maintain a competitive edge, optimizing logistics flows within the warehouse has become more critical than ever. By implementing strategic improvements, companies can significantly enhance their operational efficiency, reduce costs, and improve customer satisfaction.
Implementing Cross-Docking strategies for rapid inventory turnover
Cross-docking is a powerful logistics technique that can dramatically reduce storage time and handling costs. This strategy involves transferring incoming shipments directly from the receiving dock to the outbound shipping dock, with minimal or no storage in between. By implementing cross-docking, you can significantly accelerate inventory turnover and minimize the need for warehouse space.
To effectively implement cross-docking, consider the following steps:
- Identify suitable products for cross-docking (e.g., fast-moving items, pre-sorted shipments)
- Coordinate with suppliers for precise delivery schedules
- Implement a robust warehouse management system (WMS) to track and manage cross-docked items
- Design an efficient dock layout to facilitate smooth product flow
- Train staff on cross-docking procedures and best practices
By mastering cross-docking techniques, you can achieve faster order fulfillment , reduced handling costs, and improved inventory accuracy. This approach is particularly effective for perishable goods, seasonal items, or products with high demand volatility.
Optimizing pick path algorithms with ABC analysis
Efficient order picking is crucial for streamlining warehouse operations and reducing labor costs. By optimizing pick path algorithms, you can minimize travel time and increase picking productivity. One effective method for enhancing pick paths is through ABC analysis, which categorizes inventory based on its value and movement frequency.
Utilizing pareto principle in SKU categorization
The Pareto Principle, also known as the 80/20 rule, suggests that roughly 80% of effects come from 20% of causes. In warehouse management, this principle can be applied to inventory categorization. By classifying your SKUs into A, B, and C categories based on their sales volume or value, you can prioritize your picking strategies and optimize storage locations.
Typically, the categorization follows this pattern:
- A items: Top 20% of SKUs that generate 80% of sales
- B items: Next 30% of SKUs that generate 15% of sales
- C items: Remaining 50% of SKUs that generate 5% of sales
Integrating slotting optimization with pick path design
Once you've categorized your inventory, the next step is to integrate slotting optimization with your pick path design. Slotting optimization involves strategically placing items in the warehouse to minimize travel time and maximize picking efficiency. By combining ABC analysis with slotting optimization, you can create a highly efficient picking environment .
Consider these strategies for optimal slotting:
- Place A items in easily accessible locations near the packing area
- Group frequently picked items together to reduce travel time
- Use ergonomic principles to minimize worker strain and increase productivity
Implementing dynamic putaway strategies
Dynamic putaway is a strategy that adapts storage locations based on real-time inventory data and demand patterns. By implementing dynamic putaway, you can ensure that your warehouse layout remains optimized even as product demand and inventory levels fluctuate. This approach requires a sophisticated WMS capable of analyzing data and making real-time decisions on optimal storage locations.
Leveraging WMS data for continuous path refinement
Your WMS is a goldmine of data that can be leveraged to continuously refine and improve pick paths. By analyzing picking data, you can identify bottlenecks, optimize route sequencing, and make data-driven decisions to enhance overall warehouse efficiency. Regular analysis and refinement of pick paths based on this data can lead to significant improvements in productivity over time.
Enhancing inventory accuracy through cycle counting methodologies
Maintaining accurate inventory records is crucial for efficient warehouse operations and customer satisfaction. Cycle counting is a powerful methodology that can significantly improve inventory accuracy without the need for disruptive full-scale physical counts. By implementing strategic cycle counting techniques, you can maintain a high level of inventory accuracy year-round.
Implementing ABC-XYZ analysis for counting frequency
ABC-XYZ analysis combines the value-based categorization of ABC analysis with the demand variability assessment of XYZ analysis. This approach allows you to prioritize cycle counting efforts based on both item value and demand predictability. For example:
- AX items (high value, stable demand): Count most frequently
- CZ items (low value, unpredictable demand): Count less frequently
By focusing your counting efforts on high-value and high-variability items, you can allocate resources more effectively and maintain optimal inventory accuracy where it matters most.
Utilizing RFID technology for Real-Time inventory tracking
Radio-Frequency Identification (RFID) technology can revolutionize your inventory tracking capabilities. By implementing RFID tags and readers throughout your warehouse, you can achieve near real-time visibility of your inventory. This technology enables automated cycle counting, reducing manual labor and increasing accuracy.
Benefits of RFID in inventory management include:
- Improved inventory accuracy (up to 99.9%)
- Reduced labor costs associated with manual counting
- Enhanced visibility of inventory movement and location
- Streamlined receiving and shipping processes
Integrating cycle counting with daily operations
To maximize the effectiveness of cycle counting, integrate it into your daily warehouse operations. This approach, often referred to as "continuous cycle counting," involves counting a small subset of inventory each day as part of regular activities. By making cycle counting a routine task, you can maintain high inventory accuracy without disrupting normal operations.
Consider implementing these strategies:
- Train pickers to perform quick counts during picking activities
- Use idle time to conduct opportunistic cycle counts
- Implement a rotating schedule to ensure all items are counted at appropriate intervals
Streamlining order fulfillment with wave planning techniques
Wave planning is a sophisticated approach to order fulfillment that groups orders into "waves" for more efficient processing. This technique can significantly improve warehouse productivity by optimizing labor allocation and reducing congestion in picking areas. By implementing wave planning, you can achieve smoother workflow, reduced picking errors, and faster order turnaround times.
Key elements of effective wave planning include:
- Grouping orders based on common characteristics (e.g., shipping destination, product type)
- Balancing workload across different warehouse zones
- Coordinating picking, packing, and shipping activities
- Utilizing multi-order picking strategies to increase efficiency
To implement wave planning effectively, you'll need a robust WMS capable of analyzing order data and generating optimized waves. The system should consider factors such as order priority, inventory location, and resource availability when creating waves.
"Wave planning can increase picking productivity by up to 35% and reduce travel time within the warehouse by 50%."
When implementing wave planning, it's crucial to monitor and adjust your strategies regularly . Analyze key performance indicators (KPIs) such as units picked per hour, order accuracy, and on-time shipping rates to fine-tune your wave planning approach and maximize its benefits.
Maximizing vertical space utilization with advanced storage systems
In many warehouses, vertical space is an underutilized asset. By implementing advanced storage systems that take advantage of your warehouse's full height, you can dramatically increase storage capacity without expanding your facility's footprint. This approach not only maximizes space utilization but can also improve picking efficiency and reduce operating costs.
Implementing Automated Storage and Retrieval Systems (AS/RS)
Automated Storage and Retrieval Systems (AS/RS) are sophisticated solutions that can transform your warehouse operations. These systems use robotic cranes or shuttles to store and retrieve items from high-density storage racks, maximizing vertical space utilization and improving inventory accuracy.
Benefits of AS/RS include:
- Increased storage density (up to 85% space savings compared to traditional racking)
- Improved inventory accuracy and control
- Reduced labor costs and improved worker safety
- Faster order processing and improved throughput
While the initial investment in AS/RS can be significant, the long-term benefits in terms of efficiency gains and space utilization often justify the cost for high-volume operations.
Optimizing pallet racking configurations for density
For warehouses that primarily handle palletized goods, optimizing pallet racking configurations can yield substantial improvements in space utilization. Consider implementing high-density pallet storage solutions such as:
- Drive-in/drive-through racking for high-volume, low-SKU count items
- Push-back racking for medium-turnover items with multiple SKUs per lane
- Pallet flow racking for high-turnover items with first-in-first-out (FIFO) requirements
By selecting the appropriate racking system for different product types and implementing vertical storage strategies , you can significantly increase your warehouse's storage capacity and improve overall operational efficiency.
Utilizing mezzanines for Multi-Level order picking
Mezzanines are an excellent way to create additional floor space within your existing warehouse structure. By implementing multi-level mezzanines, you can create dedicated areas for various warehouse functions, such as order picking, packing, or value-added services. This approach not only maximizes vertical space but can also improve workflow by separating different operational areas.
When designing mezzanine systems, consider:
- Load-bearing capacity requirements
- Integration with existing material handling equipment
- Compliance with local building codes and safety regulations
- Future scalability and flexibility needs
Integrating vertical lift modules for small parts storage
Vertical Lift Modules (VLMs) are automated storage systems ideal for small parts and items. These systems consist of vertically arranged trays that are automatically retrieved and presented to the operator at an ergonomic height. VLMs can dramatically reduce the footprint required for small parts storage while improving picking accuracy and speed.
Key advantages of VLMs include:
- Space savings of up to 90% compared to traditional shelving
- Improved ergonomics and reduced worker fatigue
- Enhanced inventory control and accuracy
- Increased picking productivity
By implementing a combination of these advanced storage systems, you can create a highly efficient, space-optimized warehouse that maximizes both horizontal and vertical space utilization. This approach not only improves operational efficiency but also provides the flexibility to accommodate future growth and changing business needs.