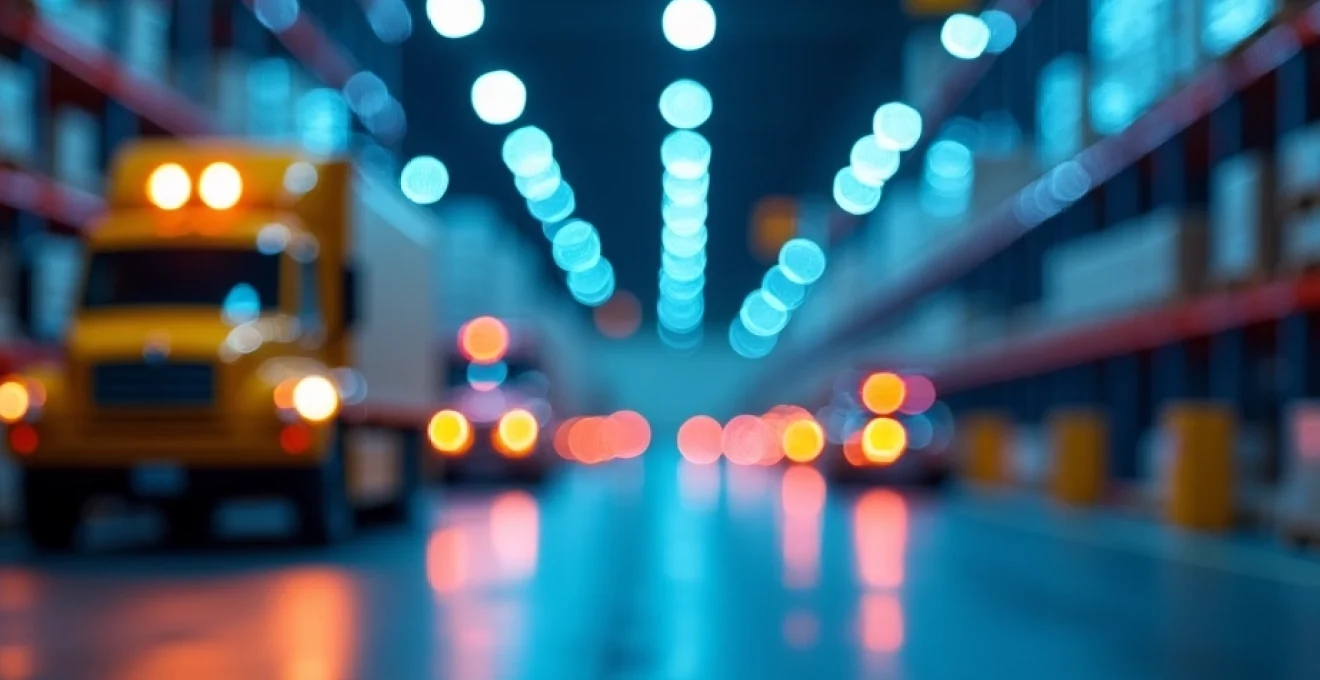
In today's fast-paced business environment, effective inventory management is crucial for maintaining a competitive edge and ensuring smooth supply chain operations. By streamlining inventory processes, companies can reduce costs, improve efficiency, and enhance customer satisfaction. This comprehensive guide explores cutting-edge strategies and technologies that can revolutionize your inventory management approach, leading to better supply chain control and overall business performance.
Inventory management system integration for supply chain optimization
Integrating a robust inventory management system is the foundation of streamlined supply chain control. Modern systems offer real-time visibility, automated processes, and data-driven insights that can significantly improve decision-making and operational efficiency. By centralizing inventory data and connecting it with other supply chain functions, businesses can achieve a holistic view of their operations and respond quickly to market changes.
One of the key benefits of an integrated inventory management system is the ability to synchronize data across multiple channels and locations. This eliminates data silos and ensures that all stakeholders have access to accurate, up-to-date information. As a result, companies can make more informed decisions about stock levels, reorder points, and demand forecasting.
Moreover, integration allows for seamless communication between different departments, such as sales, purchasing, and logistics. This improved coordination can lead to faster order fulfillment, reduced lead times, and better customer service. By automating routine tasks and workflows, employees can focus on more strategic activities that add value to the business.
Real-time data analytics in inventory forecasting
The power of real-time data analytics has transformed inventory forecasting, enabling businesses to make more accurate predictions and respond swiftly to market fluctuations. By leveraging advanced analytics tools, companies can analyze historical data, identify patterns, and generate insights that drive smarter inventory decisions.
Implementing machine learning algorithms for demand prediction
Machine learning algorithms have revolutionized demand prediction by processing vast amounts of data and identifying complex patterns that humans might miss. These algorithms can consider multiple factors such as seasonality, market trends, and external events to generate highly accurate forecasts. By implementing machine learning in inventory management, businesses can optimize stock levels, reduce carrying costs, and minimize the risk of stockouts or overstocking.
Predictive analytics powered by machine learning can also help identify slow-moving or obsolete inventory, allowing companies to take proactive measures to minimize losses. This level of precision in demand forecasting is particularly valuable in industries with volatile demand patterns or short product lifecycles.
Leveraging IoT sensors for automated stock level monitoring
The Internet of Things (IoT) has opened up new possibilities for automated stock level monitoring. By deploying IoT sensors throughout the warehouse or storage facilities, businesses can track inventory levels in real-time without manual intervention. These sensors can detect when stock falls below a certain threshold and automatically trigger reorder requests, ensuring optimal inventory levels are maintained at all times.
IoT sensors can also monitor environmental conditions such as temperature and humidity, which is crucial for perishable goods or sensitive products. This level of monitoring helps maintain product quality and reduce waste due to spoilage. Additionally, the data collected by IoT devices can be used to optimize warehouse layouts and improve overall operational efficiency.
Blockchain technology for transparent inventory tracking
Blockchain technology offers a revolutionary approach to inventory tracking by providing a secure, transparent, and immutable record of all transactions and movements within the supply chain. By implementing blockchain, businesses can create a digital ledger that tracks each item from its origin to the end consumer, ensuring complete traceability and authenticity.
This level of transparency can significantly reduce the risk of counterfeiting, theft, and fraud in the supply chain. It also enables faster and more efficient recalls if quality issues arise, as the exact location and history of each product can be quickly identified. Furthermore, blockchain can facilitate smoother collaboration between supply chain partners by providing a single source of truth for all inventory-related information.
Big data analytics tools: SAP HANA vs. Oracle Inventory Management Cloud
When it comes to big data analytics for inventory management, two industry leaders stand out: SAP HANA and Oracle Inventory Management Cloud. Both platforms offer powerful analytics capabilities, but they have distinct features that may suit different business needs.
Choosing between these platforms depends on factors such as your existing IT infrastructure, specific analytics requirements, and long-term business strategy. It's essential to evaluate each option carefully to determine which solution aligns best with your inventory management goals.
Just-in-time (JIT) inventory strategies in modern supply chains
Just-in-Time (JIT) inventory strategies have gained significant traction in modern supply chains due to their ability to reduce carrying costs and improve efficiency. By aligning inventory levels closely with production schedules and customer demand, businesses can minimize excess stock and optimize cash flow.
Toyota production system: lessons for lean inventory management
The Toyota Production System (TPS) is often considered the gold standard for lean inventory management. Its principles of continuous improvement and waste elimination have been adopted by companies across various industries. Key lessons from the TPS include:
- Focusing on pull-based production to reduce overproduction
- Implementing visual management techniques for better inventory control
- Emphasizing standardized work processes to improve efficiency
- Encouraging employee involvement in problem-solving and process improvement
By applying these principles, businesses can create a more agile and responsive inventory management system that adapts quickly to changing market conditions.
Kanban systems for Pull-Based inventory control
Kanban systems are a crucial component of JIT inventory management, providing a visual method for controlling the flow of materials through the production process. By using Kanban cards or digital signals, businesses can ensure that inventory is replenished only when needed, reducing waste and improving efficiency.
Digital Kanban systems have evolved to offer real-time visibility and automation, making them even more effective in modern supply chains. These systems can integrate with other inventory management tools to provide a comprehensive view of stock levels and production requirements.
Vendor-Managed Inventory (VMI) partnerships
Vendor-Managed Inventory (VMI) partnerships represent a collaborative approach to inventory management where suppliers take responsibility for maintaining optimal stock levels for their customers. This strategy can lead to significant benefits for both parties, including:
- Reduced inventory holding costs for the customer
- Improved demand visibility for the supplier
- Streamlined ordering processes and reduced administrative overhead
- Enhanced collaboration and stronger business relationships
Implementing VMI requires trust and open communication between partners, as well as robust data-sharing capabilities. When executed effectively, VMI can result in a more efficient and responsive supply chain.
Advanced warehousing technologies for inventory efficiency
The adoption of advanced warehousing technologies is crucial for maximizing inventory efficiency and accuracy. These technologies can dramatically improve picking speeds, reduce errors, and provide real-time visibility into warehouse operations.
Automated Storage and Retrieval Systems (AS/RS) implementation
Automated Storage and Retrieval Systems (AS/RS) represent a significant leap forward in warehouse automation. These systems use computer-controlled machines to automatically store and retrieve items from defined storage locations. The benefits of AS/RS include:
- Maximized storage density and space utilization
- Increased picking accuracy and speed
- Improved inventory tracking and control
- Enhanced worker safety by reducing the need for manual handling
While the initial investment in AS/RS can be substantial, the long-term benefits in terms of efficiency gains and reduced labor costs make it an attractive option for businesses with high-volume operations.
RFID technology for Real-Time inventory visibility
Radio Frequency Identification (RFID) technology has transformed inventory tracking by providing real-time visibility into the location and status of individual items. RFID tags can be read quickly and simultaneously, without line-of-sight requirements, making them ideal for large-scale inventory management.
The implementation of RFID can lead to significant improvements in inventory accuracy, reduced labor costs, and enhanced loss prevention. It also enables more efficient processes such as cycle counting and automated receiving, further streamlining warehouse operations.
Robotic Process Automation in warehouse operations
Robotic Process Automation (RPA) is revolutionizing warehouse operations by automating repetitive tasks and improving overall efficiency. From autonomous mobile robots that assist with picking and packing to software bots that handle data entry and order processing, RPA is transforming the way warehouses function.
The benefits of RPA in warehouse operations include:
- Increased productivity and throughput
- Reduced error rates in picking and packing
- Improved worker safety by handling hazardous or strenuous tasks
- 24/7 operation capabilities, leading to faster order fulfillment
As RPA technology continues to advance, we can expect to see even greater integration of robotics in inventory management processes.
Pick-to-light and Put-to-Light systems for order fulfillment
Pick-to-Light and Put-to-Light systems are visual aids that use LED displays to guide warehouse workers through the picking and packing process. These systems can significantly improve picking accuracy and speed, particularly in high-volume operations with a large number of SKUs.
By implementing Pick-to-Light and Put-to-Light technologies, businesses can achieve:
- Faster order fulfillment times
- Reduced training time for new employees
- Improved accuracy in order picking and packing
- Enhanced productivity through guided workflows
These systems can be integrated with existing warehouse management software to provide a comprehensive solution for inventory control and order fulfillment.
Supply chain risk management through inventory control
Effective inventory control plays a crucial role in managing supply chain risks. By implementing robust inventory management practices, businesses can mitigate various risks such as supply disruptions, demand fluctuations, and quality issues.
One key strategy for risk management is diversifying suppliers to reduce dependence on a single source. This approach can help ensure a steady supply of materials even if one supplier faces difficulties. Additionally, maintaining safety stock for critical items can provide a buffer against unexpected supply chain disruptions.
Another important aspect of risk management is scenario planning . By analyzing various potential disruptions and their impact on inventory levels, businesses can develop contingency plans to respond quickly and effectively to supply chain challenges.
Implementing a robust quality control
process throughout the supply chain is also essential for risk management. This includes regular supplier audits, incoming material inspections, and continuous monitoring of product quality. By maintaining high quality standards, businesses can reduce the risk of recalls and customer dissatisfaction.
Kpis and metrics for measuring inventory management performance
To ensure the effectiveness of your inventory management strategies, it's crucial to track and analyze key performance indicators (KPIs) and metrics. These measurements provide valuable insights into the efficiency of your inventory processes and help identify areas for improvement.
Some essential KPIs for inventory management include:
- Inventory Turnover Ratio: Measures how quickly inventory is sold and replaced over a given period
- Days Sales of Inventory (DSI): Indicates the average number of days it takes to turn inventory into sales
- Fill Rate: The percentage of customer orders that are fulfilled from available stock
- Carrying Cost of Inventory: The total cost associated with holding inventory
- Stock-to-Sales Ratio: Compares the amount of inventory on hand to the amount of sales
Regularly monitoring these KPIs can help you identify trends, set benchmarks, and make data-driven decisions to optimize your inventory management processes. It's important to establish a balanced scorecard that includes both financial and operational metrics to get a comprehensive view of your inventory performance.
Continuous improvement should be the ultimate goal of tracking these metrics. By setting targets for each KPI and regularly reviewing performance, you can drive ongoing enhancements in your inventory management practices and overall supply chain efficiency.
Implementing advanced analytics tools can help you gain deeper insights from your inventory data. These tools can identify patterns and correlations that might not be immediately apparent, allowing you to make more informed decisions about stock levels, reorder points, and inventory allocation across different locations or channels.