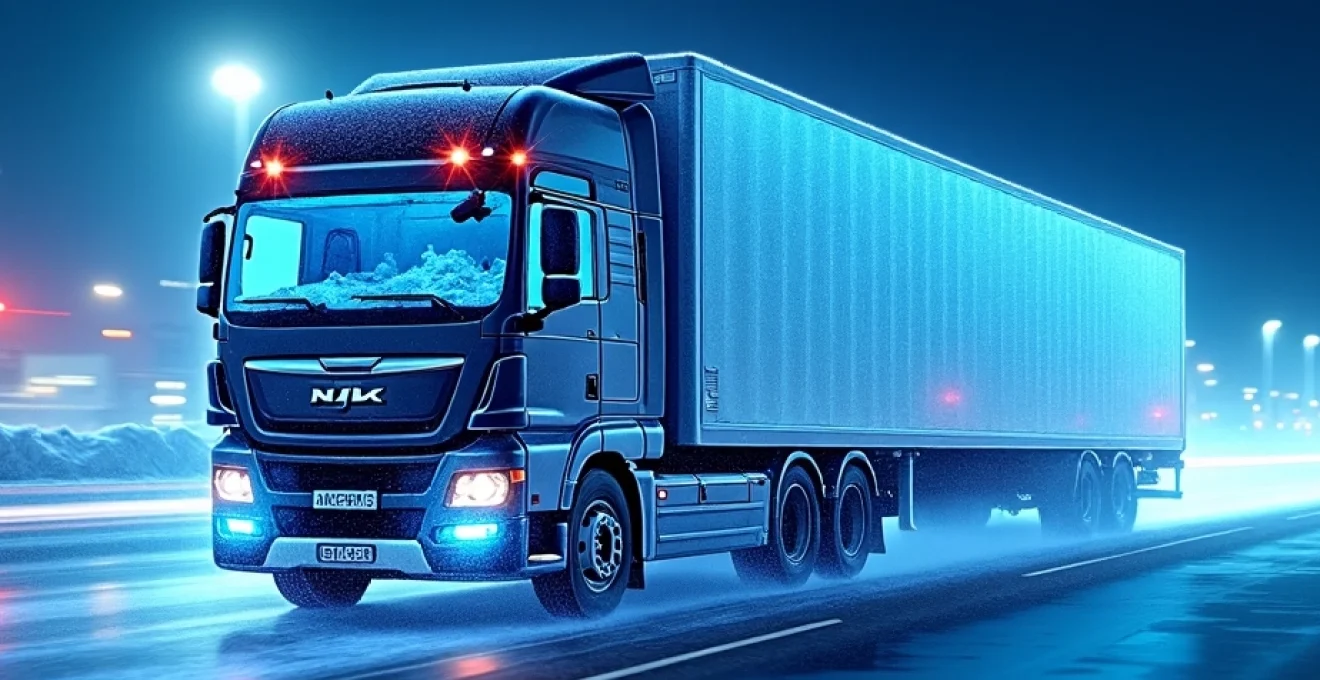
In today's globalized economy, the ability to transport perishable goods across vast distances while maintaining their quality and safety is paramount. Refrigerated transport, also known as "reefer" transport, plays a crucial role in this process, forming the backbone of the cold chain logistics system. From fresh produce and dairy products to pharmaceuticals and sensitive electronics, temperature-controlled transportation ensures that goods reach their destination in optimal condition.
The importance of refrigerated transport extends far beyond simply keeping products cold. It's a complex interplay of thermodynamics, technology, and logistics that requires constant innovation to meet the evolving demands of consumers and industries alike. As we delve into the intricacies of this vital sector, you'll discover how refrigerated transport is shaping the future of supply chains and contributing to global food security and healthcare accessibility.
Thermodynamics of mobile refrigeration systems
At the heart of every refrigerated transport unit lies a sophisticated mobile refrigeration system. These systems operate on the principles of thermodynamics, specifically the transfer of heat from one medium to another. The goal is to maintain a consistently low temperature within the cargo space, regardless of external conditions.
The basic components of a mobile refrigeration system include a compressor, condenser, expansion valve, and evaporator. The compressor pressurizes the refrigerant, causing it to heat up. As the hot, pressurized refrigerant passes through the condenser, it releases heat to the outside environment and liquefies. The liquid refrigerant then passes through an expansion valve, where it rapidly expands and cools. Finally, the cold refrigerant absorbs heat from the cargo area as it passes through the evaporator, before returning to the compressor to repeat the cycle.
One of the key challenges in mobile refrigeration is maintaining temperature stability while the vehicle is in motion and subject to varying external temperatures. This requires precise control systems and robust insulation to minimize heat transfer from the outside environment. Advanced systems may incorporate variable-speed compressors and multiple temperature zones to optimize energy efficiency and accommodate different types of cargo within the same transport unit.
Cold chain integrity: from farm to fork
The concept of "farm to fork" takes on a whole new dimension when it comes to refrigerated transport. Maintaining cold chain integrity throughout the entire journey of perishable goods is critical for ensuring food safety, preserving quality, and reducing waste. This process begins long before the goods are loaded onto a refrigerated truck or container.
Precooling techniques for perishable goods
Precooling is a crucial step in the cold chain process, particularly for fresh produce. By rapidly removing field heat from harvested crops, precooling helps to slow down the natural deterioration process and extend shelf life. There are several precooling methods used in the industry, including:
- Room cooling: Products are placed in a refrigerated room to gradually reduce their temperature.
- Forced-air cooling: Cold air is blown over and around the products to accelerate heat removal.
- Hydrocooling: Products are immersed in or sprayed with chilled water to rapidly lower their temperature.
- Vacuum cooling: Products are placed in a vacuum chamber, where evaporative cooling rapidly reduces their temperature.
The choice of precooling method depends on the type of product, its physical characteristics, and the desired cooling rate. Effective precooling not only prepares goods for transport but also helps to reduce the load on the refrigeration system during transit.
Thermal mapping in reefer containers
Ensuring uniform temperature distribution within a refrigerated container is essential for maintaining product quality. Thermal mapping is a technique used to identify hot spots or cold spots within the container that could potentially compromise the integrity of the cargo. This process involves placing temperature sensors at various points throughout the container and monitoring temperature fluctuations over time.
The data collected from thermal mapping can be used to optimize loading patterns, adjust airflow, and fine-tune refrigeration settings. For example, you might discover that products loaded near the doors are more susceptible to temperature fluctuations during loading and unloading. Armed with this knowledge, you can implement strategies such as using insulating curtains or adjusting the stacking pattern to mitigate these risks.
Last mile delivery: maintaining temperature control
The final leg of the journey, known as "last mile" delivery, presents unique challenges for temperature-controlled logistics. As goods are transferred from large refrigerated trucks to smaller vehicles for local distribution, maintaining the cold chain becomes increasingly complex. Innovations in this area include:
- Portable refrigeration units that can be easily transferred between vehicles
- Insulated packaging solutions that maintain temperature for short periods without active cooling
- Route optimization software that minimizes time spent in transit
- Temperature-controlled lockers for contactless delivery of perishable goods
These solutions help ensure that the cold chain remains unbroken right up to the moment of delivery, preserving the quality and safety of temperature-sensitive products.
Iot sensors for Real-Time cold chain monitoring
The Internet of Things (IoT) has revolutionized cold chain monitoring by enabling real-time tracking of temperature, humidity, and other critical parameters throughout the entire journey. IoT sensors placed within refrigerated containers or attached to individual packages can transmit data to cloud-based platforms, allowing for continuous monitoring and rapid response to any deviations from the desired conditions.
This level of visibility not only helps prevent spoilage but also provides valuable data for optimizing the entire cold chain process. By analyzing patterns and trends in temperature fluctuations, you can identify areas for improvement in your refrigerated transport operations, leading to increased efficiency and reduced costs.
Refrigerated transport modes and technologies
The refrigerated transport industry employs a diverse range of technologies and transport modes to meet the varied needs of different products and supply chains. From long-haul trucking to intermodal containers and specialized air freight solutions, each mode of transport has its own unique advantages and challenges when it comes to temperature control.
Thermo king vs. carrier: reefer unit comparison
Two of the leading manufacturers in the refrigerated transport industry are Thermo King and Carrier. Both companies offer a wide range of refrigeration units for trucks, trailers, and containers. While they share many similarities, there are some key differences in their approaches to technology and design.
Thermo King is known for its robust, fuel-efficient units that often incorporate advanced features such as telematics and remote monitoring capabilities. Carrier, on the other hand, has a reputation for innovation in refrigerant technology and has been at the forefront of developing more environmentally friendly cooling solutions.
When choosing between Thermo King and Carrier units, consider factors such as:
- Energy efficiency and fuel consumption
- Cooling capacity and temperature range
- Maintenance requirements and service network availability
- Compatibility with your existing fleet management systems
- Initial cost vs. long-term operating expenses
Ultimately, the best choice will depend on your specific operational needs and the types of goods you transport.
Cryogenic refrigeration in Long-Haul transport
For long-haul transport of highly temperature-sensitive goods, cryogenic refrigeration offers an alternative to traditional mechanical refrigeration systems. This technology uses liquid nitrogen or carbon dioxide as a refrigerant, which is stored in a tank on the vehicle and released into the cargo area as needed to maintain the desired temperature.
Cryogenic systems offer several advantages for certain applications:
- Rapid temperature pull-down capabilities
- Precise temperature control, even at extremely low temperatures
- Quieter operation compared to mechanical systems
- Reduced maintenance requirements due to fewer moving parts
However, cryogenic systems also have limitations, including the need for regular refilling of the cryogenic fluid and potential safety concerns associated with handling these extremely cold substances. As such, their use is typically limited to specialized applications where their unique benefits outweigh these drawbacks.
Eutectic plate systems for urban distribution
In urban environments where noise regulations may restrict the use of engine-driven refrigeration units, eutectic plate systems offer an effective alternative. These systems consist of metal plates filled with a eutectic solution that freezes and thaws at a specific temperature. The plates are frozen overnight while the vehicle is plugged into a power source, and then maintain a stable temperature throughout the day's deliveries without the need for a running engine.
Eutectic systems are particularly well-suited for multi-drop deliveries in urban areas, as they:
- Operate silently, allowing for nighttime and early morning deliveries
- Maintain consistent temperatures even when doors are frequently opened
- Require no fuel during operation, reducing emissions and operating costs
- Offer reliable performance with minimal maintenance
While eutectic systems have limitations in terms of temperature range and cooling capacity compared to mechanical systems, they play an important role in the urban distribution of temperature-sensitive goods.
Phase change materials in passive cooling solutions
Phase Change Materials (PCMs) are substances that absorb or release large amounts of energy as they change from solid to liquid or vice versa. In refrigerated transport, PCMs are used in passive cooling solutions to maintain stable temperatures without the need for active refrigeration systems.
PCM-based solutions typically involve encapsulating the material in panels or pouches that are placed around the cargo. As the ambient temperature rises, the PCM absorbs heat as it melts, keeping the surrounding area cool. When the temperature drops, the PCM solidifies, releasing heat and preventing the cargo from getting too cold.
These passive cooling solutions are particularly useful for:
- Short-duration transports where active refrigeration may not be practical
- Backup temperature control in case of mechanical refrigeration failure
- Enhancing temperature stability in conjunction with active cooling systems
- Reducing energy consumption by supplementing mechanical refrigeration
As PCM technology continues to advance, we can expect to see more innovative applications in refrigerated transport, potentially revolutionizing how we approach temperature control in certain logistics scenarios.
Regulatory compliance in Temperature-Controlled logistics
The refrigerated transport industry is subject to a complex web of regulations designed to ensure food safety, product quality, and environmental protection. Compliance with these regulations is not just a legal requirement but also a key factor in maintaining customer trust and protecting public health.
One of the most important regulatory frameworks in this field is the Food Safety Modernization Act (FSMA) in the United States. The FSMA includes specific requirements for the sanitary transportation of human and animal food, mandating that shippers, carriers, and receivers of food products take steps to prevent contamination during transport. This includes maintaining appropriate temperature controls and keeping records of temperature monitoring throughout the journey.
In Europe, the Agreement on the International Carriage of Perishable Foodstuffs and on the Special Equipment to be Used for such Carriage (ATP) sets standards for the international transport of perishable foodstuffs. The ATP specifies the types of vehicles and equipment that can be used for transporting different categories of perishable goods and defines the temperature conditions that must be maintained.
Compliance with these regulations requires careful attention to detail and investment in appropriate technology and training. Some key areas of focus include:
- Implementing robust temperature monitoring and recording systems
- Ensuring proper cleaning and sanitization of transport vehicles
- Training personnel in food safety practices and temperature control procedures
- Maintaining accurate documentation of all transport activities
- Regularly calibrating and maintaining refrigeration equipment
By prioritizing regulatory compliance, refrigerated transport operators not only avoid potential legal issues but also contribute to a safer and more reliable cold chain for all stakeholders.
Energy efficiency and sustainability in refrigerated transport
As concerns about climate change and environmental sustainability grow, the refrigerated transport industry is under increasing pressure to reduce its carbon footprint. This has led to a wave of innovations aimed at improving energy efficiency and reducing emissions across the cold chain.
Solar-powered auxiliary power units for reefer trucks
One promising development in this area is the use of solar-powered auxiliary power units (APUs) for reefer trucks. These systems use solar panels mounted on the roof of the trailer to generate electricity, which can be used to power the refrigeration unit or other onboard systems. This reduces the need for the truck's engine to idle when stationary, saving fuel and reducing emissions.
Solar APUs are particularly effective in sunny climates and for operations that involve frequent stops or long periods of stationary time. While the initial investment in solar technology can be significant, the long-term benefits in terms of fuel savings and reduced maintenance costs make it an attractive option for many fleet operators.
Aerodynamic design for fuel efficiency in refrigerated trailers
Improving the aerodynamics of refrigerated trailers can significantly reduce fuel consumption, especially for long-haul operations. Manufacturers are incorporating features such as:
- Rounded corners and smooth side panels to reduce air resistance
- Trailer skirts to minimize airflow underneath the trailer
- Rear fairings to reduce turbulence behind the trailer
- Low-rolling-resistance tires to decrease road friction
These aerodynamic enhancements can lead to fuel savings of 5-15%, depending on the specific design and operating conditions. When combined with other efficiency measures, the cumulative effect can be substantial, both in terms of cost savings and environmental impact.
Telematics for route optimization and fuel management
Advanced telematics systems are revolutionizing the way refrigerated transport fleets operate, providing real-time data on vehicle performance, route efficiency, and driver behavior. By analyzing this data, fleet managers can optimize routes to minimize fuel consumption and reduce idle time.
Telematics can also help improve refrigeration unit performance by:
- Monitoring compressor run time and cycling patterns
- Alerting operators to potential maintenance issues before they become critical
- Optimizing defrost cycles based on actual operating conditions
- Providing insights into temperature stability and identifying areas for improvement
By leveraging telematics data, refrigerated transport operators can significantly reduce their environmental impact while also improving operational efficiency and reducing costs.
Future trends: electrification and autonomous refrigerated vehicles
The future of refrigerated transport is likely to be shaped by two major trends: electrification and autonomous vehicles. These technologies have the potential to dramatically reduce emissions, improve efficiency, and revolutionize the way temperature-sensitive goods are moved around the globe.
Electric refrigerated trucks are already being tested and deployed in various markets, offering zero-emission operation and lower noise levels compared to diesel-powered units. As battery technology continues to improve and charging infrastructure expands, we can expect to see wider adoption of electric refrigeration systems, particularly for short and medium-haul operations.
Autonomous vehicles present exciting possibilities for the refrigerated transport sector. Self-driving trucks could potentially operate 24/7, optimizing route efficiency and reducing labor costs. When combined with advanced refrigeration systems and IoT sensors, autonomous vehicles could provide unprecedented levels of control and monitoring throughout the cold chain.
However, the transition to these new technologies will not be without challenges. Issues such as range limitations for electric vehicles, regulatory hurdles for autonomous systems, and the need for significant infrastructure investments will need to be addressed. Nevertheless, the potential benefits in terms of sustainability, efficiency, and product quality make these trends worth watching closely.